LUBExpert
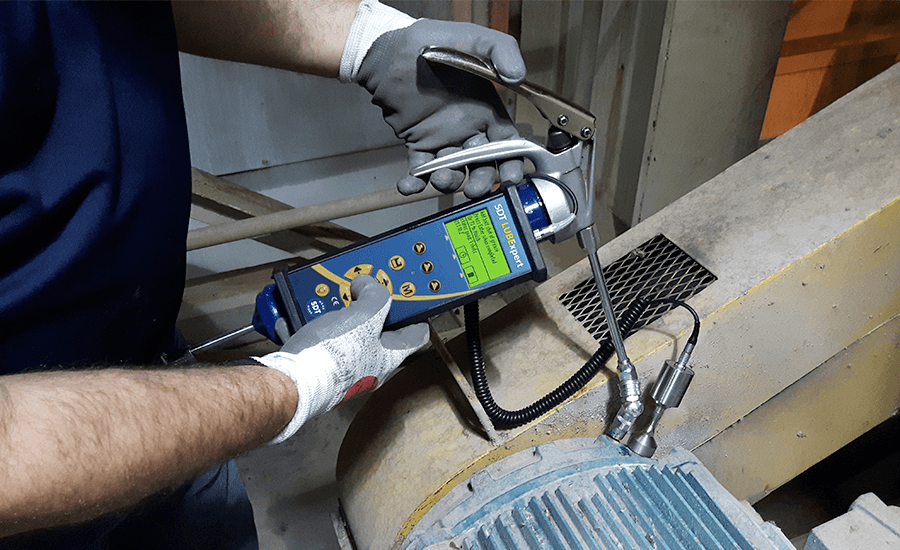
Grease Bearings right with the SDT LUBExpert
Machinery lubrication remains the single biggest factor affecting asset reliability, and it is still one of the most misunderstood maintenance tasks performed in industry. When machinery lubrication is done incorrectly the results can be devastating. But when done correctly, manufacturers can expect long, trouble-free life from their bearings. Therefore, manufacturers should seek a better machinery lubrication solution… they should seek LUBExpert.
When bearings fail unexpectedly, production grinds to a halt and the last thing manufacturers need to worry about is the price of replacing a single failed bearing. They must consider what processes have been affected, how long the downtime is going to take, if they even have the proper spares on location to make the necessary repairs, and what the total cost of downtime is going to be.
Even today, with the many advancements in maintenance coming with modern manufacturing techniques, data, and systems, so many machinery lubrication departments still grease their bearings on a wasteful calendar and formula-based schedule. Re-lubrication strategies based on formulae and calendars are the norm in industry and they were the best science we had before ultrasound. But using time-based strategies can lead to bearings being over-greased and under-greased. Therefore, a condition-based approach must be implemented for optimal bearing lubrication.
Why doesn’t Calendar/Formula-Based Machinery Lubrication Work?
Most bearing manufacturers provide end-users with a grease replenishment formula for each of their bearings. So, picture there are two identical bearings from the same OEM. One ends up in a hot and humid paper mill outside of São Paulo, Brazil… The other, in the frigid climate of Northern Ontario’s, Kirkland Lake, at a gold mine. Would these bearings require the same re-greasing schedule? Probably not.
The following machinery re-lubrication formula factors in bearing housing temperature, roughly how much contamination there is, moisture, vibration, positioning, bearing design, RPM, and bore diameter… There are a lot of different measurements and calculations that need to be made to ensure the bearing’s grease intervals are correct and they need to be re-taken all the time to ensure accuracy. Surely this isn’t the best way to calculate greasing intervals… There must be a better way.
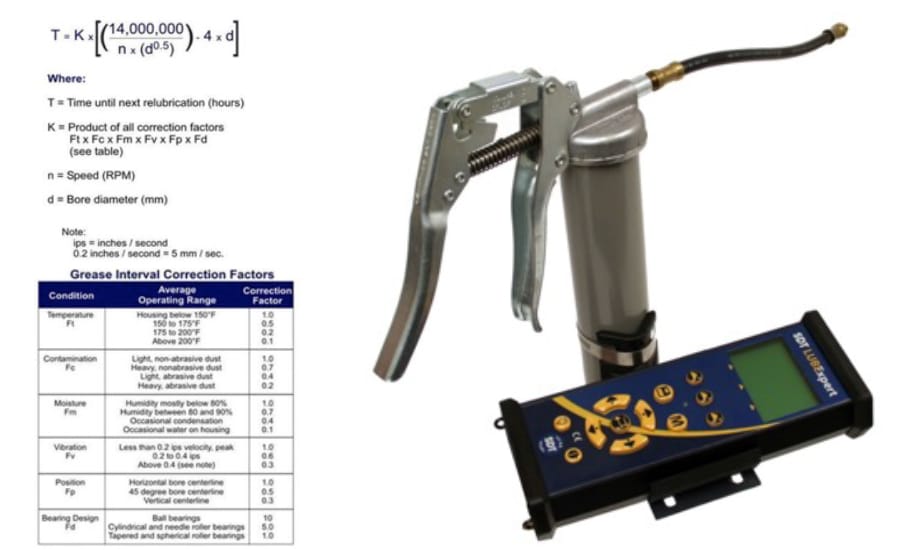
UAS3 LUBExpert Bearing & Asset Database, Shopping Lists, Work Orders, Greasing Modes
Organize your entire lubrication reliability strategy with Ultranalysis® Suite 3. Manage, trend, and analyze all of your ultrasound, vibration, and lubrication data using UAS3.
Rotating Asset Database
Your UAS3 Asset Database is your lubrication reliability roadmap. The seven level, tree structured hierarchy gives lube techs exact directions in navigating to their lubrication replenishment points. With multiple data folders, technicians have best in class condition monitoring organization, for even the most complex factory layouts.
Bearing Database
LUBExpert maintains your bearing database. Technicians can keep tabs on all the bearings in their facility. This includes bearing types and make, dimensions, grease compatibility, and much more.
Work Orders
LUBExpert’s Work Orders are set up within UAS3 to serve technicians as a reminder for which bearings need to be greased and when based on historical condition monitoring data.
LUBExpert Guided and Free Modes
Remove the guesswork using LUBExpert’s Guided mode and let SDT’s Bearing Lubrication Algorithm determine optimal regreasing quantity.
Know your assets inside and out? Grease your bearings with LUBExpert’s Free Mode.
How LUBExpert Helps you Grease Bearings Right
Right Lubrication
Different bearings and applications require different lubrication. Some lubricants are made up of oil, some are grease, which is a mixture of oil and thickener (usually lithium-based soap), some lubricants are dry to avoid dust and dirt… Some lubricants can’t survive high temperature applications, and a lot of greases aren’t compatible.
It is not as simple as grabbing the nearest grease gun and pumping random lube into a bearing. LUBExpert’s onboard assistant helps technicians select the correct grease and reminds them of the bearing’s maximum capacity.
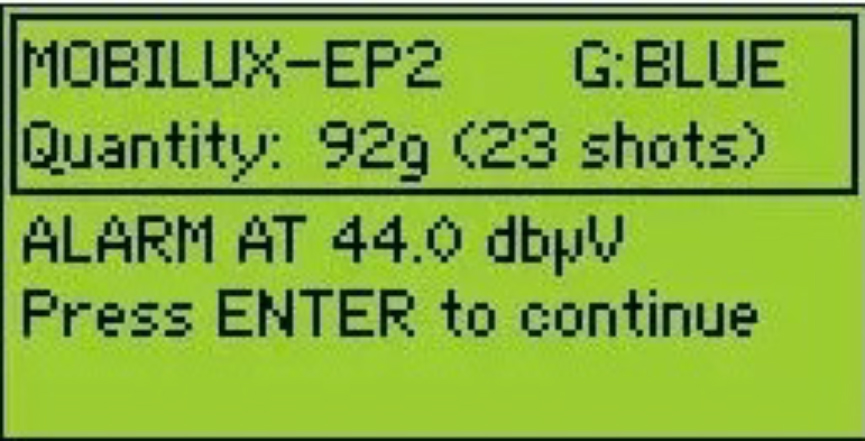
The Right Location
An average lube technician might have thousands of bearings under management. Using the asset database in UAS3, technicians need not worry whether they’re greasing the right bearings. LUBExpert’s onboard assistant guides them through the plant, ensuring they arrive at the correct asset, with the correct grease, at the correct time.
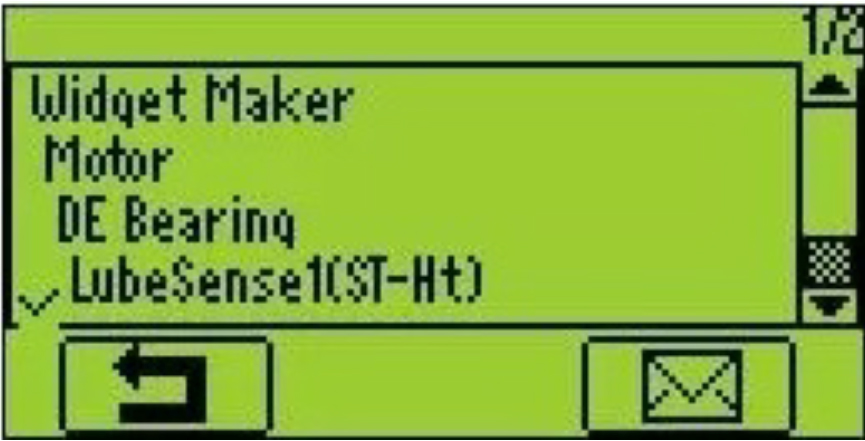
The Right Interval
While condition-based bearing re-lubrication is the optimal method for increasing bearing lifespan, LUBExpert and UAS3 accommodate both condition and calendar-based re-lubrication schedules. Based on parameters set by the lube technician, which can be based on historical data, or time interval since the last lubrication replenishment task, alarms can be set up and triggered to ensure bearings are greased at the right time.
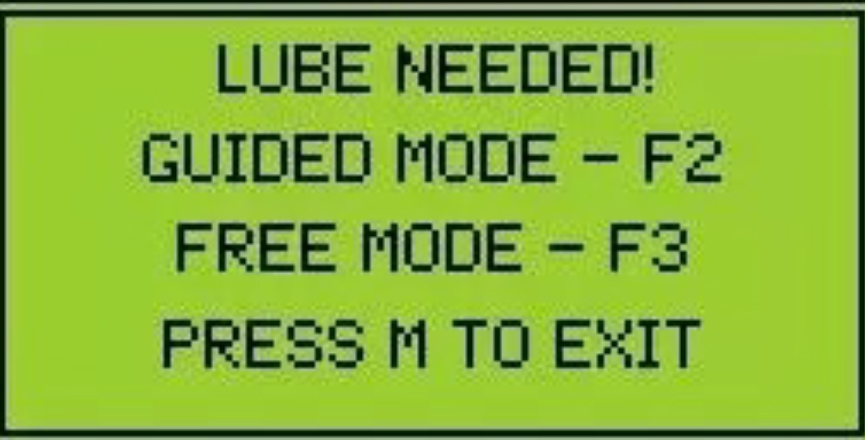
The Right Quantity
When a bearing fails prematurely, lube techs can usually look to over or under lubrication as the cause. While this lubrication error typically stems from calendar-based re-lubrication schedules, it can sometimes still occur using a condition-based lubrication solution. Especially if the technician hasn’t selected the correct bearing greasing tool for the job…
Technicians need not worry with LUBExpert. In action, LUBExpert’s onboard assistant is continuously recalculating friction levels between half shots of grease, to determine whether or not to add more. Using historical data, LUBExpert’s onboard assistant alerts lube technicians when optimal friction levels have been reached.
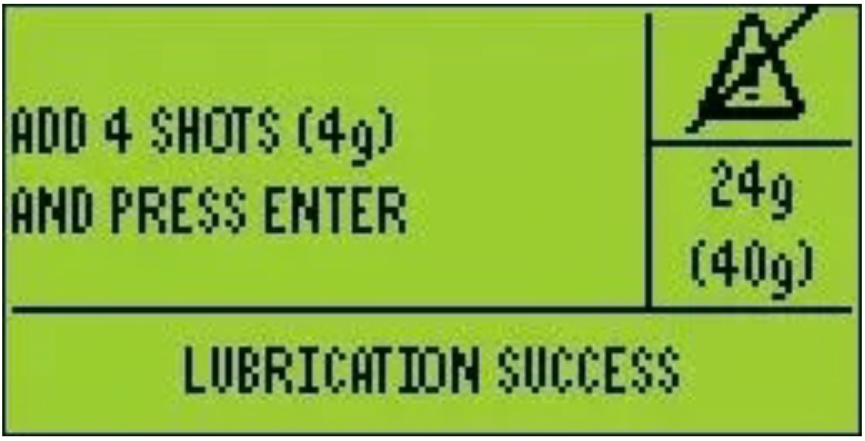
The Right Indicators
Lube technicians can be confident when re-greasing bearings with LUBExpert’s onboard assistant smoothly guiding them through lubrication tasks from start to finish. After each lubrication replenishment task, lube techs receive a GOOD, BAD, or SUSPECT result to determine whether or not their lubrication task was a success.
Lubrication tasks results are tied back into UAS3, where reports can be generated to illustrate the health of the bearings on that task, grease consumption per department, total grease consumption.
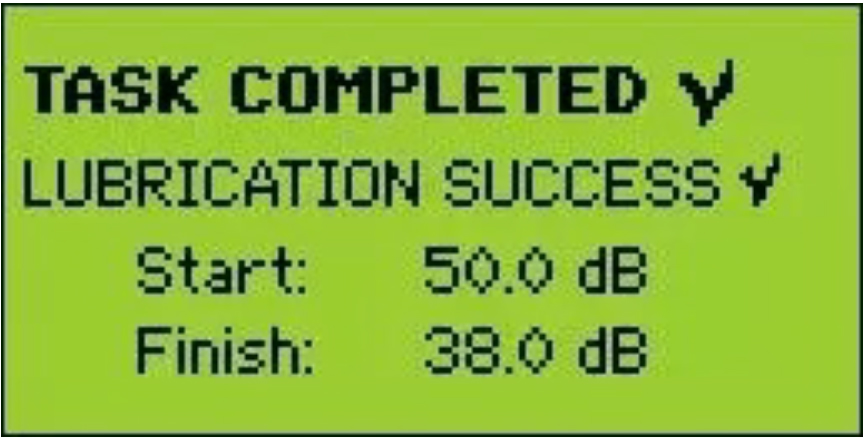
LUBExpert Dynamic Option
Collect valuable, dynamic condition monitoring data with LUBExpert Dynamic and analyze it in UAS3. When the lubrication team can collect, and view data in the Time and Frequency domain they can remove silos between them and the condition monitoring team.
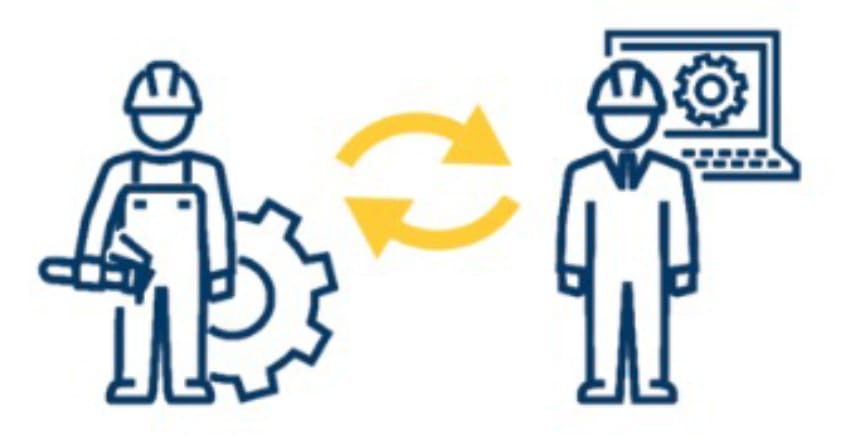