Why more Lubrication Programs are Opting for Ultrasound over Time-Based Formulas
While performing a condition-based lubrication route, our customer, a Lubrication Technician at a Canadian Pulp & Paper Plant recorded the following two measurements on one of their critical motors. In Figure 1, we observe the Ultrasound FFT before the grease injection, and in Figure 2 we can see the effect the grease injection had on the asset.
When taking the initial measurement as seen in Figure 1, the technician noticed lots of impacting listening through his headphones.
Examining the ultrasonic FFT closer in UAS3, we observe high energy levels which could indicate elevated friction and the need for lubrication. We can also see the repetitive impacting that was noticed by the technician while listening through their headphones.
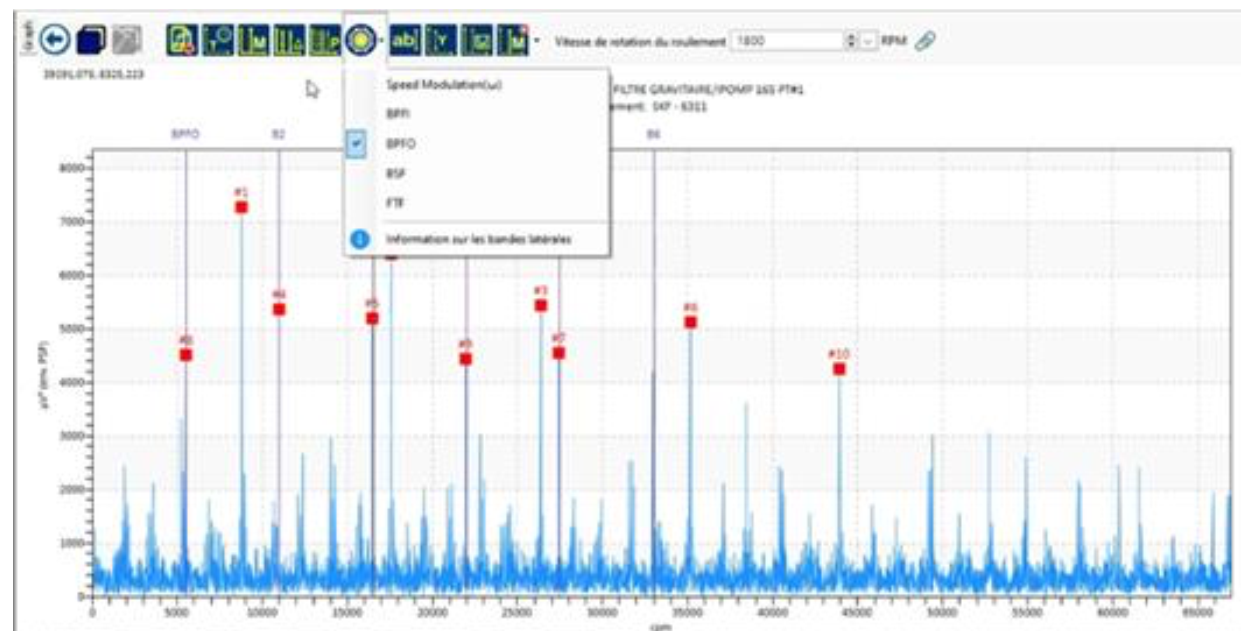
In Figure 2, we observe the ultrasonic FFT after the grease injection. The energy levels have dropped significantly, which is an indicator that friction has decreased; however, we still see lots of repetitive impacting, most likely meaning the bearing is broken.
Using the Bearing Toolbox Ultrasound Fault Frequency Calculator, an add on to the UAS3 software, the technician was able to determine that this bearing had a ball pass frequency outer race defect. It will be monitored closely and replaced the next planned shutdown.
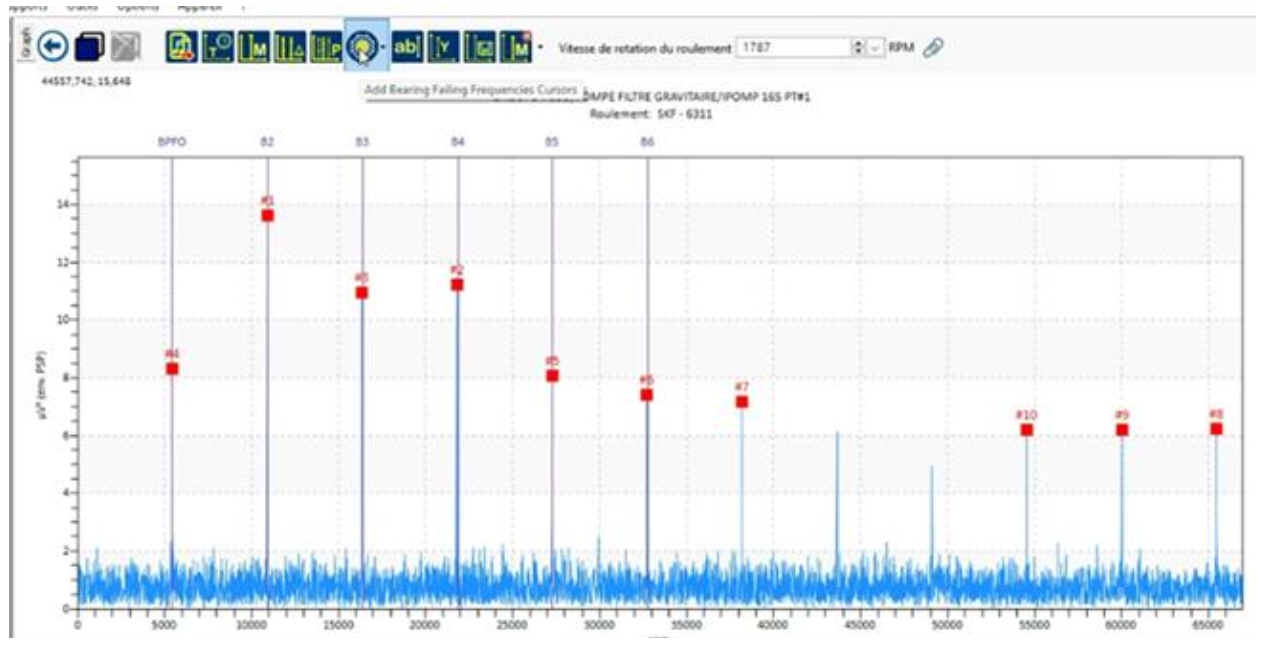
The Bearing Toolbox is a database made up of over 50,000 bearing references and fault frequencies. By matching rotational speed and bearing dimensions to the ultrasound emitted from a rotating asset, the Bearing Toolbox can determine different types of common bearing defects.
The additional analysis capabilities of utilizing ultrasound while replenishing grease to a bearing is what sets it apart from traditional time-based lubrication formulas.
Sure, adding a few shots of grease to this bearing would still have reduced friction and even improved the assets condition for a small duration of time, but what it won't do is fix the bearing fault. Without ultrasonically listening to the bearing or taking a closer look at the data in UAS3, the technician likely wouldn't have discovered this fault.